Wellstrøm’s unique well plugging tool concept uses electrical heating that enables close control and monitoring of the alloy barrier setting process. Furthermore, the bespoke-designed high power deployment cable incorporates fibre-optic and CCL technology, facilitating depth control and close monitoring and verification of barrier installation.
The heater can be recovered from the newly-set alloy barrier, allowing the plug to be internally verified by ultrasonic logging technology.
This ensures precision alloy wellbore sealing unlike any other solution curently on the market, and delivers a comprehensive barrier solution demanded by clients operating in the most stringently-regulated regions of the world.
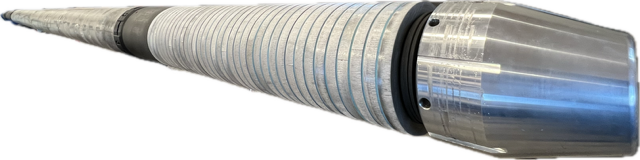
Electrical heating for high precision barrier installation
- The tool is lowered into the well on a high-power cable. The tool incorporates CCL for depth control, and fibre optic and thermocouple sensing to precisely determine the source of inflow and also monitor the plug-setting process in real time, enabling the plug to be set with a high degree of accuracy.
- Once in position, the heating system is activated to melt the bismuth alloy. The high-density molten alloy flows downwards until it cools and solidifies around the based of the mandrel which acts as a heat sink, forming a “casting platform”. The remaining alloy builds up on the platform, and penetrates perforations, cracks and fissures down to the mircometer scale. Upon cooling to the ‘solidification isotherm’ the alloy instantly solidifies and expands, forming a tenacious gas-tight seal.
- Once the alloy plug has solidified, the toolstring can be recovered, leaving the plug behind to form a high durable wellbore barrier.
- The plug has been confirmed capable of forming a high differential pressure seal, even when set in drilling fluid and flowing gas.
Watch CEO Gert Rege explaining the tool and each component.
Unique Features
Control: Wellstrøm utilizes electrical methods with closely-controlled and heating cycles to precisely install alloy seals: there is no need for ‘one shot’ pyrotechnics, resulting in complete control of alloy melt and placement. Furthermore, the depth and real-time monitoring capability enables the sealing process to be executed reliability and definitively, without the risk of damage to outer wellbore barrier elements, such as annular cement and caprock formations.
Precision: Wellstrøm’s alloy plug can be reliably set in most fluids found in challenging downhole environments, including in flowing gas. In addition, the fluidity of the bismuth alloy is such that the liquid metal will penetrate the narrowest of apertures, resulting in complete sealing of the wellbore and a seamless gas-tight seal.
Reliability: The engineered alloys and designs used by Wellstrøm are creep-resistant and highly durable, creating a gas-tight seal.
Cost and C02 footprint reduction: Our sealing concepts offer the potential for significant cost savings, removing the need for costly rig-based operations whilst delivering higher integrity outcomes and reduced C02 footprint, with an estimated 45% lower C02 emissions from manufacturing to the point of delivery.
Key Differentiators
- Wellstrøm’s designs utilise >25 years of industry-leading R&D expertise in alloy sealing technologies
- Unique patented ‘ribbed’ mandrel designed to ‘lock’-in the solidified alloy, maximise radial contact stress and arrest alloy creep
- Mandrel design can accept ultrasonic logging tools to enable azimuthal barrier placement verification
- Bespoke high-power cable deployment system incorporating CCL and fiber optic sensing technology for depth control, real-time monitoring and verification. Deployment possible to depths in excess of 4000 m / 13,000 ft
- Full-scale tested in flowing gas and drilling fluid to high differential pressures
- Proven to be capable of remediating failed annular cement and Sustained Casing Pressure and provide a high differential pressure seal
- Barrier placement process demonstrated to be fully controllable, monitorable and repeatable. Tool design uniquely able to re-melt and re-set alloy if required
- High corrosion and creep resistance providing extreme seal durability in downhole environments
- Barrier design intended to comply with OEUK, NORSOK and DNV RP-A203 guidelines (qualification ongoing)
Designed for operators — based on their fundamental requirements!